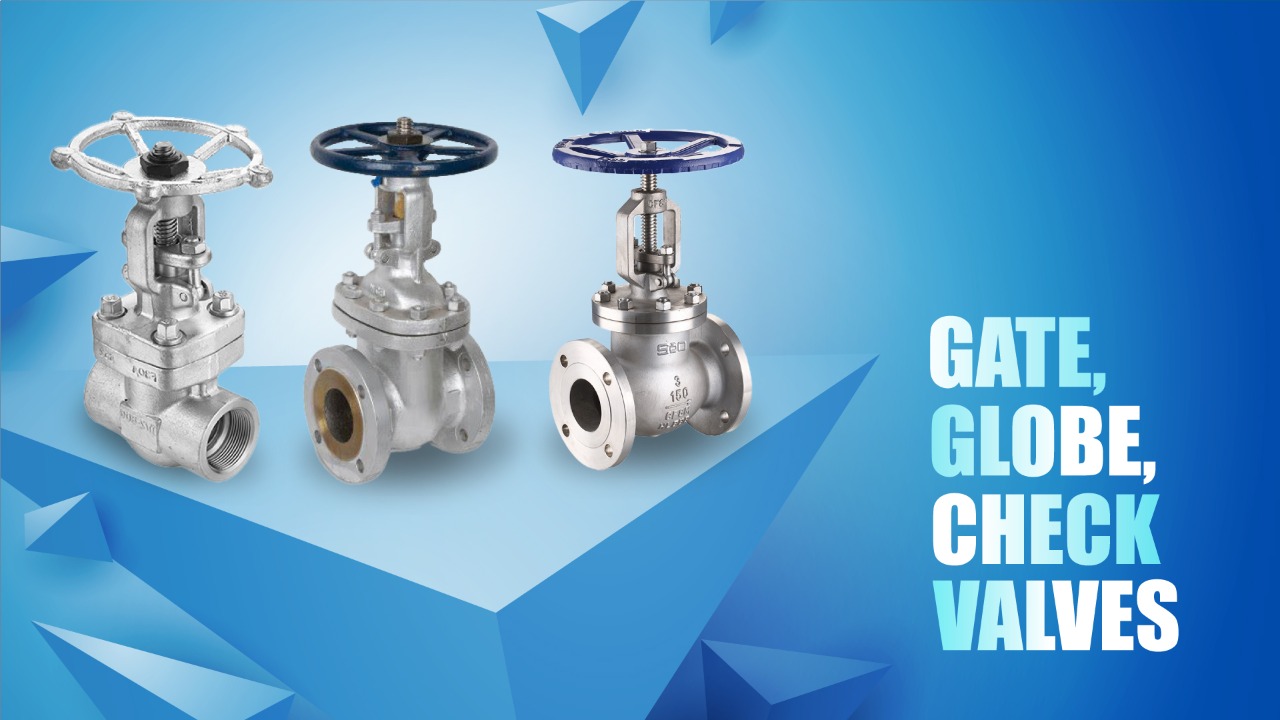
Industrial Valves Guide
Detailed Industrial Valves Guide by Mangalam Industrial Products
Industrial valves are one of the most significant components used in many industries including the oil and gas industry, manufacturing, water treatment and others. They maintain, guide, and manage the processes involving the movement of fluids, gases along with slurries which, in turn, lead to the proper running of the process. It’s important to understand that the operation and safety of such industries depend on several factors, including the quality and durability of the industrial valves.
Selecting the right industrial valve is one of the most important aspects of ensuring that industrial processes are effective and incident-free. Mangalam Industrial Products has a niche in delivering superior-quality industrial valves to the industry.
Importance of Quality in Industrial Valves
In industrial operations, the availability and operating safety of equipment are very important factors that cannot be compromised. Industrial valves are manufactured for use in industries where conditions are very harsh and equipment needs to work continuously without any failure. Good valves do not allow leakage, can regulate the flow without errors and shield systems from possible threats. The selection of higher quality valves can reduce the occurrence of operational hitches thus ensuring the safety of employees and other equipment in the plant.
It is understandable that high quality industrial valves can be a bit expensive in the first place, but then again they are even more cost-efficient than low quality counterparts in the long run. Long-lasting valves also mean that they are replaced and repaired more rarely thus cutting on the costs of maintenance. Also, with the help of effective flow control, resources are used most efficiently, and thus decrease operational costs. In the case of maintenance, quality valves can reduce overall system downtime and improve productivity, which makes this investment a sound one in the long run.
The fact of the matter is that the compliance to standards and regulatory measures is very important in any industrial venture. High quality industrial valves are produced according to certain industry guidelines in terms of the specifications and standards required for the valve. By applying valves that meet these standards, the performance is assured, but more importantly, the regulations that may create problems such as fines and laws are averted.
Things to know about Industrial Valve
Industrial valves are used to open, close or regulate the flow of fluids within a system; these include liquids, gases and many more. These valves play critical roles in regulating industrial processes through controlling the rate of flow, act as isolation devices, and prevent flow reversal.
Types of Industrial valves
Manifold Valves: Manifold valves are those equipments used in handling multiple valves compactly in one system. They are essential in circumstances where the flow stream is complicated and are widely employed in the oil and gas industries.
Non-Return Valves (NRV): Commonly referred to as check valves, NRVs are designed to open and close to facilitate flow in only one direction. They are commonly used in water and wastewaters applications as safeguards for equipment and systems stability.
Ball Valves: These are well-known for their long-lasting as well as high levels of sealing capabilities whereby the element of control is a ball. It is best for use in application where a rapid rundown or very fast shut off is needed and widely used in chemical and oil and gas market.
Globe Valves: It is specifically designed for accurate control of the flow of the fluids, and it operates based on a linear movement. These are mostly applied in applications that need frequent and intermittent control like in steam, oil and gas industries.
Check Valves: These specific valves help to avoid backflow and allow the medium to move only in the required direction. These check valves are used in several fields, namely the chemical processing industry, water treatment plants, and power plants.
Needle Valves: Needle valves have slow flow characteristics which make them ideal for use in flow calibration situations. They are widely applied to those industrial processes that need precise control of the flow, for example, instrumentation and gas supply industries.
Mono Flange Valves: Mono flange valves are installed where several functions are joined in one unit, thereby decreasing the overall need for multiple valves and fittings. They are equally very useful in areas such as offshore and petrochemical industries mainly because of the factors of space and weight.
Various application of Industrial Valves
Valves are a crucial element in many industries and functioning of other industrial products. In the oil and gas sector, they oversee the transportation and treatment of crude oil and natural gas via pipelines and processing facilities. In the chemical industry they help in safe handling and processing of different chemicals in industries. Water and wastewater treatment plants use valves for the indication of water flow or for the control of flows of sewage. Similarly, the power generation plants require industrial valves that control the steam or the cooling water systems to work safely and optimally.
Factors to Consider
Material: The type of material from which the valve is made should be compatible with the fluid that is to be controlled. Stainless steel, brass, and PVC are materials that are frequently used for these purposes and each has its own uses depending on the specific use that is required.
Size: Flow and pressure also depend much on sizing, especially when a particular channel needs to be scaled to meet specific parameters. Make sure is an easy integration of the valve within the system piping.
Pressure and Temperature Ratings: When selecting a valve, ensure that it is capable to handle the maximum pressure and temperature within your system so that you don’t have valve failure or damage.
Type of Fluid: Think about the flowing characteristics like, viscosity, corrosive nature and the amount of solids in the fluid. There is a way that various types of valves are working effectively in controlling different fluids.
Maintenance and Longevity of Industrial Valves
Industrial valves require regular maintenance to have a longer service time in the plant and perform effectively. Maintenance is not only important to increase the valves’ lifespan but also to avoid having high expenses such as lost time and possible dangers in industries. Maintenance is required to be done periodically as industrial valves are essential for the proper functioning of various operations. Regular and proper servicing aids in identifying any possible flaws in time before they form significant complications.
Valves that maintain properly are work efficient that control flow without interruption. Regular inspections enable to spotting wear and tear early and avoid unplanned failures. Maintaining safety standards in Industrial settings depends on well-operating valves.
Tips for maintenance
Investigate visually on a regular basis to look for leaks, water damage or wear. Check unusual noises or vibrations, which may point serious problems. Make sure there is sufficient lubrication on all moving parts. A well-lubricated valve lasts longer and doesn't rust. Impurity causes blockage and damage, so keep valves clean. Make sure you can use appropriate cleaning techniques and methods suited to the valve material. Double check and tighten all connections and fittings to stop leaks.
Loose connections can lead to pressure drops and inefficient operation. Perform functional tests regularly to check that the valves open and close properly. Test the valves under normal operating conditions to verify their performance. Keep a detailed documentation about maintenance record, noting all inspections and replacements. This helps in tracking the valve’s history and planning future maintenance schedules.